Lập kế hoạch nhu cầu nguyên vật liệu
- 31 thg 5, 2024
- 7 phút đọc
Đã cập nhật: 31 thg 12, 2024
Lệnh sản xuất mới
Sau đây sẽ giới thiệu cách tạo lập lệnh sản xuất:
Đơn sản xuất có thể được tạo trực tiếp từ đơn hàng tiêu thụ hoặc kế hoạch nhu cầu nguyên vật liệu (MRP). Các đơn sản xuất được tạo sẽ được liên kết với mã đơn hàng tiêu thụ hoặc mã đơn hàng sản xuất nội bộ.
Phương pháp khác là tạo đơn sản xuất từ dự án. Nguyên tắc này tương tự tạo đơn sản xuất từ nhu cầu nguyên vật liệu MRP. Và sẽ không giới thiệu nguyên tắc đó vào phần này.
1. Tạo đơn sản xuất từ hạng mục đơn hàng
Số lượng sản xuất được tính dựa trên số lượng sản xuất của đơn hàng. Đơn hàng thường là đơn hàng tiêu thụ, đơn hàng mẫu hoặc đơn hàng sản xuất nội bộ. Người dùng có thể sử dụng tiêu chí tìm kiếm để lọc.
Sau khi chọn hạng mục đơn hàng, nhấn vào nút Tạo đơn MO để tạo đơn sản xuất
Nếu người dùng muốn tự động tạo đơn dựa trên công thức quy trình sản xuất, người dùng nhấp chọn tại cột “Tự động tạo MO”. Khi đơn sản xuất được tạo, hệ thống sẽ phát sinh nhu cầu nguyên vật liệu đầu vào.
Đơn sản xuất đầu vào tự động tạo dựa vào nhu cầu vật liệu của công thức quy trình sản xuất. Và vật liệu không cần thiết lập là Tắt MRP.
Sau khi tạo đơn sản xuất thành công, hệ thống sẽ chuyển đến màn hình “Lệnh sản xuất phác thảo”. Nhấn vào Mã đơn sản xuất để chỉnh sửa.

Đơn sản xuất có thể được tạo từ các đơn hàng tiêu thụ cụ thể. Vui lòng tham khảo hướng dẫn ở phần quản lý đơn đặt hàng.
2. Tạo đơn sản xuất từ MRP
Trong màn hình này, nhu cầu cho mỗi loại vật liệu sẽ được tính toán theo công thức của hệ thống. Khi có nhu cầu, khối lượng sản xuất cần thiết sẽ được hiển thị, và dữ liệu nguyên liệu cơ bản phải được thiết lập để đáp ứng phương thức nhu cầu như một đơn hàng. Ví dụ, loại hàng tồn kho là bán thành phẩm:
Điền vào tiêu chí tìm kiếm như Mã vật liệu, sau đó nhấp vào các mặt hàng người dùng muốn tạo đơn MO và nhấp vào “Xác nhận yêu cầu”.
Đánh dấu vào ô "Tính toán ngày nhu cầu đầu tiên " và nhấn nút tìm kiếm, kết quả tính toán nhu cầu sẽ được lưu trữ trong vật liệu.
Tính toán ngày nhu cầu đầu tiên để tự động tạo đơn hàng sản xuất vật liệu. Khi đơn đặt hàng sản xuất được tạo ra bởi MRP này, sẽ có nhu cầu về nguyên liệu đầu vào. Các đơn hàng sản xuất sẽ tự động tạo đầu vào dựa trên nhu cầu MRP về nguyên liệu.
Người dùng có thể thấy hệ thống tự động tạo đơn sản xuất nguyên liệu
Sau khi tạo xong, màn hình sẽ chuyển sang tab " Lệnh SX phác thảo".

Mỗi vật liệu có thể không có đơn sản xuất vì quy trình sản phẩm chưa được thiết lập, hoặc có thể phát sinh nhiều đơn sản xuất vì nhiều vật liệu chia sẻ cùng nguyên liệu đầu vào.
Giới hạn trên và dưới của nhu cầu MRP là khoảng nhu cầu tìm kiếm, tương ứng với các điều kiện tìm kiếm như mã vật liệu, loại vật liệu, phân loại vật liệu, phân loại vừa, phân loại chi tiết vật liệu và số lượng MRP.
"Tính lại MRP" có nghĩa là khi đơn MRP được tạo ra, hệ thống sẽ tính toán lại các yêu cầu vật liệu và cập nhật chúng vào dữ liệu vật liệu cơ bản.
"Tự động ký duyệt đơn SX" có nghĩa là khi đơn đặt hàng sản xuất MRP được tạo ra, đơn đặt hàng sản xuất sẽ tự động được phê duyệt và chuyển sang trạng thái hoạt động.
"Tự động lên lịch đơn SX" có nghĩa là khi lệnh sản xuất từ MRP được tạo ra, đơn sẽ tự động được phê duyệt sang trạng thái tiến hành và đợt quy trình sản xuất sẽ được tạo tự động, đây là cách lên lịch đơn giản
Sau khi chọn hạng mục trong kết quả tìm kiếm và chọn quy trình để tự động thực hiện sau khi tạo đơn sản xuất, người dùng có thể nhấn "Xác nhận yêu cầu". Hệ thống sẽ tạo ra MO dựa trên "Số lượng MO từ MRP". Số lượng này cũng có thể được điều chỉnh thủ công trước khi tạo đơn hàng.
Nếu người dùng muốn kiểm tra nguồn gốc của nhu cầu MRP, người dùng có thể nhấp vào chi tiết nhu cầu để xem.
Màn hình sẽ được chuyển đến chi tiết yêu cầu. Người dùng chỉ có thể thực hiện duy nhất một tra cứu.
Vui lòng tham khảo phần giới thiệu ở các chương tiếp theo.
3. Tạo đơn sản xuất từ MRP theo Nhà máy
Thiết lập của màn hình này tương tự như nội dung trước, chỉ có thêm Mã nhà máy có sẵn để tra cứu, vì vậy người dùng có thể tham khảo mô tả trước đó.
4. Yêu cầu chi tiết
Trong chi tiết yêu cầu, người dùng có thể xem thông tin tính toán nhu cầu MRP. Các chi tiết của từng giá trị được liệt kê theo các yếu tố của công thức MRP. Lấy ví dụ này làm giải thích. Người dùng thấy là Hạn chót. Bảng này liệt kê tất cả các yếu tố ảnh hưởng đến nhu cầu. Giá trị tích lũy cuối cùng, được sắp xếp theo nhu cầu và thời gian mong muốn, chính là số lượng yêu cầu.
Từ hình trên, người dùng có thể thấy rằng tổng nhu cầu của vật liệu này đến thời điểm phát sinh là -165,766.866. Số lượng âm cho thấy có nhu cầu, vậy đó có nghĩa là số lượng yêu cầu MRP là 165,766.866
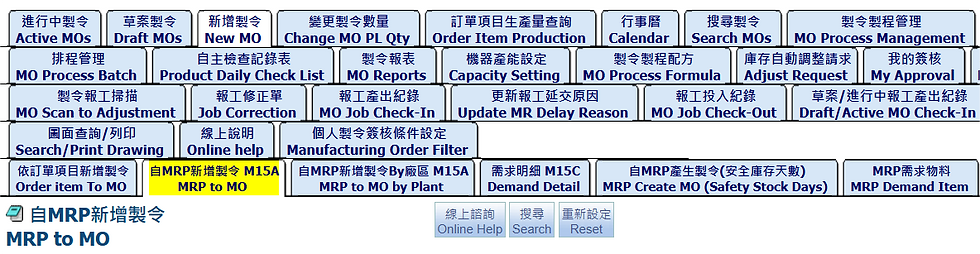
Các yếu tố được liệt kê trong kế hoạch nhu cầu có thể được tra cứu trong chi tiết các phần bên dưới, như tra cứu tồn kho sẵn có.
Tra cứu công thức sản xuất yêu cầu
5.Tạo đơn sản xuất (Ngày tồn kho an toàn)
Đơn sản xuất có thể được tạo dựa trên số ngày tồn kho an toàn
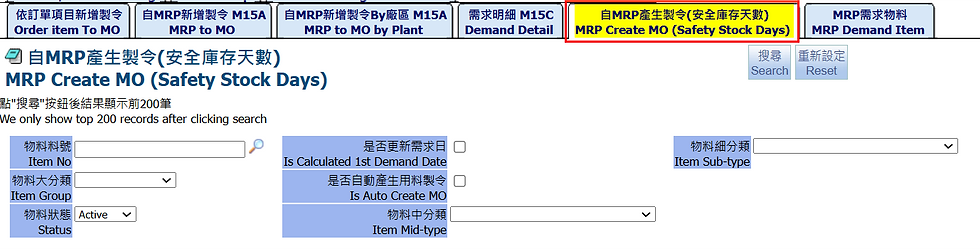
Đầu tiên, thiết lập số ngày tồn kho an toàn trong màn hình chỉnh sửa nguyên liệu, ví dụ: nguyên liệu 4FE020001
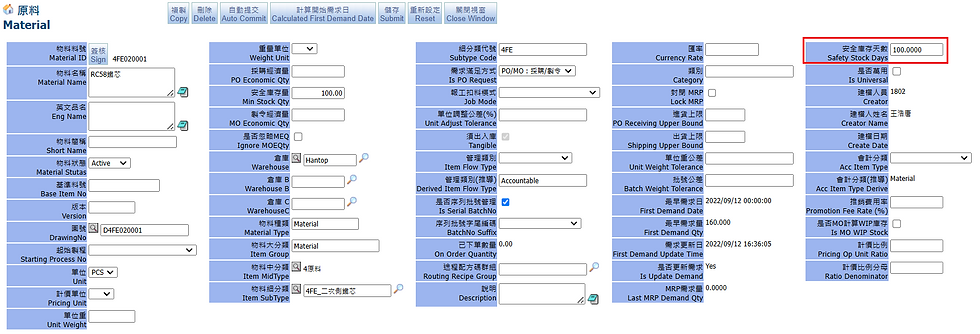
Quay lại trang “Tạo đơn sản xuất (Ngày tồn kho an toàn)”, người dùng có thể thấy số ngày tồn kho an toàn của mã vật liệu 4FE020001 đã được thiết lập, điền vào số lượng đặt hàng và nhấn Xác nhận yêu cầu.

Hệ thống thông báo đã tạo MO từ MRP thành công
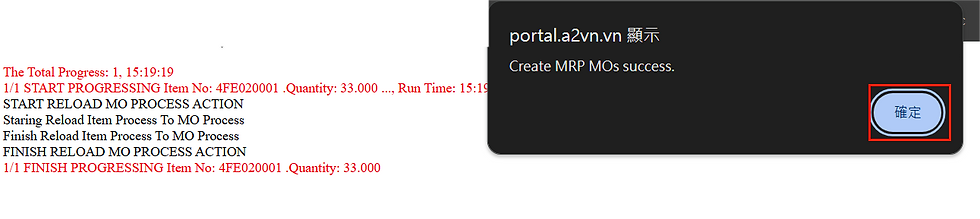
Sau khi tạo xong màn hình sẽ chuyển sang màn hình Lệnh sản xuất phác thảo. Nhấn Tìm kiếm để xem lệnh sản xuất đã tạo, số lượng dự kiến (MO Planned Qty) = 33 cái

6.MRP nhu cầu sản phẩm
Màn hình này người dùng có thể truy vấn thông tin liên quan đến vật liệu cần thiết của MRP


7. Công thức MRP
Trong phần trước, việc tạo lệnh sản xuất từ MRP đã đề cập đến việc hệ thống hiển thị chi tiết của từng yếu tố. Tiếp theo sẽ giới thiệu cách mà những yếu tố này được kết hợp thành công thức:
Công thức MRP:
X = IM + (SA - IM2SA) + MFD - IM2MFD - CS – POB – MOB - SAS + MS + SAPSOutput – SAPSInputB
If X > 0 then (if IgnoreMOEQty = 1 then MRP Qty = X else MRP Qty = max(X,MEQ) ) else MRP Qty = 0
Dưới đây là định nghĩa của từng hệ số:
Số lượng sản xuất nội bộ (IM) lưu ý: Đơn hàng sản xuất nội bộ do MRP tạo không bao gồm đơn sản xuất nội bộ (IM) ở trạng thái draft, active và trạng thái hạng mục đơn hàng là draft, active hoặc rỗng.
Số lượng đơn hàng tiêu thụ (SA): hạng mục đơn hàng trạng thái đang tiến hành
IM2SA: (đơn hàng sản xuất nội bộ IM liên kết với đơn hàng tiêu thụ SA)
Trạng thái của SA: Đang hoạt động và trạng thái mục đơn hàng: nháp, hoạt động, rỗng
max(số lượng IM liên kết với SA – số lượng IM liên kết với MO)
SAPSOutput: Hạng mục đầu ra dịch vụ sản xuất của SA
SAPSInputB: Hạng mục đầu ra dịch vụ sản xuất của SA – Số lượng dịch vụ sản xuất đã nhận
Tồn kho hiện tại (CS) = Tồn kho của mặt hàng – tồn kho mặt hàng lỗi Xem: ViewItemStockFT và ViewInvItemRealTimeStock
Số dư PO: (POB) Trạng thái của PO: nháp, tiến hành và trạng thái của hạng mục PO: nháp, tiến hành, rỗng
Số dư PO = Số lượng lên lịch xin mua - Số lượng hạng mục PO đã nhận
Số lượng còn lại MO: (MOB) Trạng thái của MO: nháp, tiến hành
Số lượng = Số lượng sản xuất - số lượng hoàn thành
Công thức nhu cầu MO (MFD) Trạng thái của MO: nháp, tiến hành và trạng thái quy trình MO: nháp, tiến hành, rỗng.
Số lượng = số lượng đầu vào x (1 + Sản phẩm tiêu hao x 0,01) – số lượng đã sử dụng cho sản xuất
Số lượng đơn bán hàng đã giao: (SAS) Lưu ý: chỉ dành cho đơn bán hàng đang tiến hành >> lấy số lượng giao hàng (Trạng thái của đơn SD = Closed)
IM2MFD = max( số lượng liên kết với MFD – IMMOQTY, 0) (LOGIC HIỆN TẠI)
Trạng thái IM và trạng thái MO = Active (Đang tiến hành)
Số lượng hàng tồn kho tối thiểu (MS)
Số lượng kinh tế sản suất (MEQ)
8. Ví dụ tính số lượng MRP
Ví dụ: mã hàng : 3RPN100050108001, số lượng MRP = 302,256
Kế hoạch nhu cầu như sau:
Công thức MRP:
X = IM + (SA - IM2SA) + MFD - IM2MFD - CS – POB – MOB - SAS + MS + SAPSOutput – SAPSInputB
If X > 0 then (if IgnoreMOEQty = 1 then MRP Qty = X else MRP Qty = max(X,MEQ) )
else MRP Qty = 0
Chi tiết nhu cầu MRP:
Số lượng nhu cầu MRP = IM + (SA - IM2SA) + MFD - IM2MFD - CS – POB – MOB - SAS + MS + SAPSOutput – SAPSInputB
= 600,000 + (0 – 0) + 304,456 – 0 – 0 – 302,000 – 300,200 – 0 + 0 + 0 – 0 = 302,256
Hết.