NKUST synergizes resources from industry, academia, and research to create the "Advanced Stamping Mold Process Technology Service Operation and Promotion Platform" ,Upgrade high-end manufacturing
- Jun 3, 2024
- 5 min read
Updated: Feb 3
2023/10/06 Great News|張淑慧
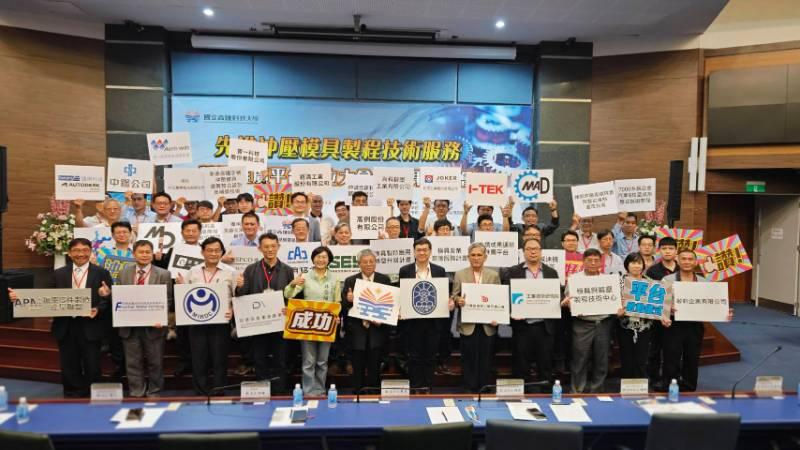
For Taiwan's mold industry to evolve towards higher quality and customization, it will require enhanced manufacturing intelligent design, expedited prototype testing, and comply with advanced manufacturing processes conditions etc. Industrial Development Administration,Ministry of Economic Affairs(MOEA) and Taiwan Mold & Die Industry Association cooperate, forge a synergy between industry, academia, and research in the south to infuse the mold industry with the necessary technological advancements and talent cultivation for high-end. manufacturing.
In 2023, Industrial Development Administration, MOEA launched the "Mold Industry Advanced Manufacturing Upgrading and Transformation Plan", delegating the promotion of this initiative to the Industrial Technology Research Institute(ITRI). On the October 6, the "Advanced Stamping Mold Process Technology Service Operation Promotion Platform hosted a Conference and Achievements Presentation" at the National Kaohsiung University of Science and Technology(NKUST). This event aims to furnish the mold industry with essential technical guidance and talent development in the stamping domain. Furthermore, it anticipates generating a synergistic cluster effect, fostering connections within the mold industry across southern Taiwan.

Including Zhao-Zhong Guo, head of the Industrial Development Administration, MOEA;
Zhen-Yuan Gao, Deputy Director-general of Economic Development Bureau, Kaohsiung City Government;Hong-Ming Xie, Vice Chairman of Taiwan Mold & Die Industry Association;
Dai-Hua Lin, Legislator、Qi-Chang Xie, Dean of Industry-Academia Collaboration of NKUST, they are main promoter of new material forming plan;Chong-Tian Lin, Director of Fine Forming R&D Department, Metal Center;Xiang-Yuan Ding, business manager of Mechanical and Mechatronics Systems Research Labs;Bor-Tsun Lin, Director of Metal Product Development Technology R&D Center、Jun-Zhi Guo, CEO、Zong-Liang Wu, Head of Mechanical and Electrical Department, NKUST,the event was graced by the presence of over a hundred esteemed guests from various sectors, including industry, government, academia, and research. In addition, many scholars and experts from the NKUST、National Formosa University、Industrial Technology Research Institute(ITRI)、 and Metal Center also gave presentations.The venue also featured exhibition booths, which showcased the sophisticated advancements and high-end manufacturing upgrades achieved by the mold industry in the stamping sector over recent years.
Ching-Chang Lien, Director of the Industrial Development Administration, MOEA, said the high-end mold sector is characterized by a significant technical threshold. Domestic manufacturers, constrained by scarce resources, frequently encounter critical bottlenecks in their transformation efforts. This situation, compounded by the dual crisis of technological deficiencies and talent shortages, has paved the way for academic and research institutions to step in and offer their services. NKUST's technical prowess is adept at addressing three pivotal themes:"Digital Mold Development", "Advanced Metal Forming Technology", and "Manufacturing Process Monitoring". It is well-equipped to offer sophisticated technical services in these areas.

Winner of the National Industry-Academic Master Award-- Bor-Tsun Lin, Chair Professor, he said the evolving paradigms of net zero carbon emissions and Industry 4.0 are placing increasing pressure on manufacturers around the world to transform. It has become crucial to upgrade digitalization, intelligence, and technological progress that is conducive to low-carbon operations. This is also an important goal of the stamping forming team of NKUST in recent years.Advancing in the realms of sophisticated forming technology and nurturing talent are crucial factors that determine the industry's competitive edge in securing international orders.
Qi-Chang Xie, Dean of Industry-Academia Collaboration of NKUST, he said NKUST, headed by the College of Intelligent Mechanical and Electrical Engineering, The college has a team of 180 teachers specializing in mechanical molds, distributed in the Department of Mechanical Engineering, the Department of Mold and Die Engineering, and the Department of Mechanical and Electrical Engineering, for the mold industry in southern Taiwan, it is a very strong technical upgrading coaching team. NKUST is pivotal in connecting industry, academia, and research resources, fostering the integration and formation of industrial clusters. The adjacent Metal Industries Research & Development Centre(MIRDC) research institution serves as a vital collaborator in academia, working in tandem to bolster the advancement of industrial technology upgrades.
Qi-Chang Xie emphasized, "Advanced stamping mold manufacturing process technology service operation and promotion platform", beyond its technical service capabilities, the platform offers comprehensive one-stop solutions encompassing technology and personnel training. It spans the spectrum from information dissemination to technological expertise, and from nurturing talent to market expansion. This initiative serves the proximate mold industry and fortifies the research and development, as well as the innovative prowess, of regional industrial clusters.
At the venue, National Formosa University presented "Harmonic Gear Near-Net Servo Forging Process Development Technology" ;the Metal Center demonstrated "Smart stamping die rapid design technology","Virtual and real integrated design and compensation technology of multi-curved iron handle bracket mold", "Chain belt stamping production line construction and integrated post-heat treatment technology"; ITRI demonstrated "7000 series aluminum alloy automotive B-pillar warm forming integrated technology" etc.

The team of Bor-Tsun Lin、Chair Professor and Jun-Zhi Guo, Associate Professor,demonstrating "harmonic reducer flexspline process optimization technology"、"Aluminum alloy material hot extrusion molding development technology" and "Smart manufacturing can use technology in the stamping industry" on the spot.
The team has honed its expertise in a suite of advanced technologies within the stamping domain, including automatic loading, unloading, and material handling, automatic soldering, seamless mold changing, precision measuring, and predictive maintenance. This proficiency ensures the timely upkeep and replacement of molds and equipment, streamlining the entire manufacturing process.Within the production line's PLC control system, it boasts capabilities in software design, MODBUS communication, human-machine interface implementation, and program editing. These competencies are integral to the sophisticated orchestration of the manufacturing process.The team has successfully implemented an unmanned stamping automatic production line, embracing the innovative concept of a 'lights-out factory', which signifies a fully automated and human-independent manufacturing environment.The technology plays a pivotal role in elevating and transforming Taiwan's industrial machinery landscape, bolstering the international standing of Taiwan's machinery sector in high-end manufacturing systems. This advancement not only generates significant economic impact but also broadens the industry's application markets considerably.
The Metal Center team provides invaluable assistance to the mold company by constructing and integrating advanced post-heat treatment technology into the chain belt stamping production line, a process that has garnered considerable attention for its innovation. Jiang-Ming Wei, Director of the Metal Center Precision Forming Group, said upon integrating this technology, the stamping production line is now capable of operating in a continuous stamping mode at a rate of 10 to 15 strokes per minute (spm), enhancing efficiency and productivity. Following the heat treatment process, the finished product achieves a hardness exceeding HRC45 and maintains a dimensional accuracy within the stringent standard of ≤0.2mm. Simultaneously, the technology is capable of precisely forecasting and adjusting for quenching deformation, thereby rectifying the dimensions of medium carbon steel workpieces that have been altered during the heat treatment process. This ensures that the final product meets exacting specifications with remarkable accuracy.