Elementary Modules
It has 24 main modules based on object-oriented concepts. Each module has a clear user interface design. It can also be customized by industry, organization and need, and adapted quickly for future changes.
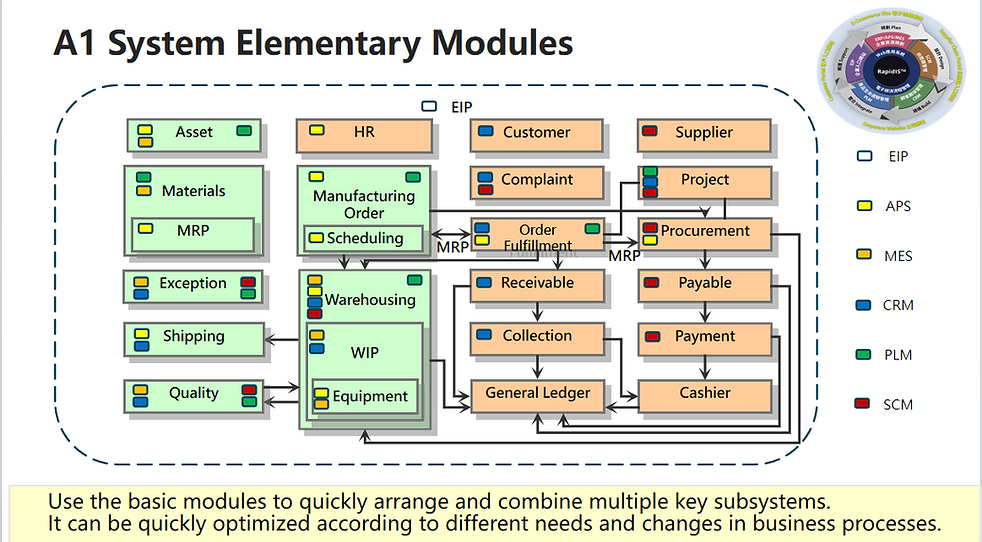
M01. Customer Management
The Customer Management Module efficiently centralizes customer data, ensuring seamless management of key details and interactions. It mitigates business risk by unifying records and adheres to privacy laws, enhancing data security and trust.

M03. Order Management
The Order Management Module is tailored to manage various sales order types with precision and ease. It ensures all relevant records are accessible and streamlines the process of forwarding essential documents. Moreover, it provides accurate cost estimations to optimize financial planning.

M05. Collection Management
The Collection Management Module offers a comprehensive solution for monitoring and managing payments. It allows for real-time checks of uncashed notes, overdue amounts, and collections under specific conditions. The module simplifies pre-receipt tasks, manages multi-currency transactions, and integrates payment details with bank records, ensuring accuracy and financial integrity.


M06. Procurement Management
The Procurement Management Module enhances the procurement process by fully integrating inquiries and orders, streamlining internal purchases, and automating approvals. It ensures efficient material requirement planning and links all related document records for seamless operations.
M07. Payables Management
Manage and Track Payables Easily
• Generate reversal operations in batches for all transaction accounts
• Transfer to accounts payable based on actual warehousing quantity
• Carry forward those without warehousing records (such as expenses) according to purchase order items
• Handle various non-purchase expenditure operations, such as payroll, expenses, etc.
• Break down income types by payable items
• Process downstream payments and subpoenas differently by payable types
• Record the many-to-many relationship between suppliers' unified invoices and accounts receivable clearly
• Provide real-time statistics and detailed list of accounts payable for any period by manufacturer, payment status, and unified invoice
• Print each supplier's statement in batches
• Automatically approve by financial department if the amount of various categories exceeds the limit
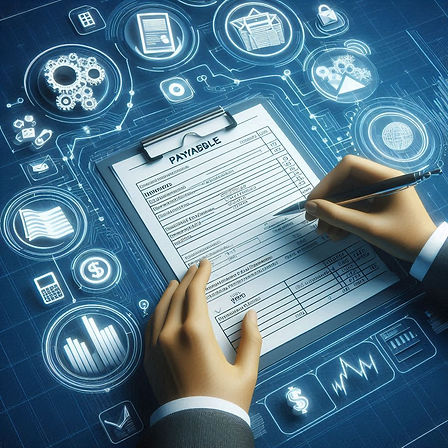
M08. Payment Management
Manage Prepayments and Payments Easily
-
Record prepayment deductions and refunds clearly
-
Check the latest balance anytime
-
Handle multi-currency transactions for any manufacturer, with separate accounts by currency
-
Handle various discounts and overpayments, such as purchase discounts, purchase and withdrawal discounts, etc.
-
Break down income types by payable items
-
Adjust amounts without payable items by user
-
Process downstream subpoenas differently by payment type
-
Integrate payment details with bank-managed transaction records, and check the actual records and balance of each account instantly
-
Record all accounts payable, payments, and discounts fully

M09. General Ledger Management
Automate and Streamline Accounting Process
• Transfer internal receipts/payments, warehouse entry/exit, bank cashier operations, fixed asset value changes, etc. into subpoenas automatically in batches
• Provide fast many-to-many reversal function and query instant reversal records anytime
• Provide bulk posting function
• Display and classify relevant upstream and downstream information of each document or subpoena on the same page
• Limit the input and viewing range precisely by different states
• Distinguish different types of subpoenas and provide different approval and check procedures
• Provide flexible and secure management processes to ensure financial information safety and accuracy
• Integrate receivables, payables, and collection and payment information automatically and provide managers with the latest account status
Provide financial statements for any date range flexibly, such as:
• Journal
• Daily balance
• Accounts receivable subsidiary ledger
• General ledger
• Subsidiary ledger
• Cash book
• Balance of real account detail lists
• Trial balance
• Income statement
• Balance sheet
• Property directory lists
• Depreciation query
• Balance of bank account
• Detailed transactions search
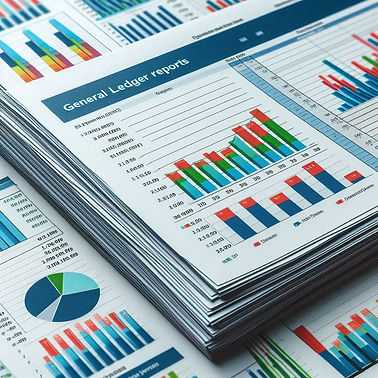
M10. Cashier Management
Manage Eight Types of Transaction Documents
-
Cash withdrawal: transaction records of petty cash account payments
-
Check withdrawal: check payments, with different statuses of bill payment, cashing, etc.
-
Remittance withdrawal: transaction records of account transfer/remittance payments
-
Cash deposit: transaction records of petty cash account receipts
-
Check deposit: transaction records of check receipts, with different statuses of bill collection, cashing, etc.
-
Remittance deposit: transaction records of account transfer/remittance receipts
-
Cash transfer withdrawal/deposit: transaction records of account transfers
-
Cash adjustment withdrawal/deposit: transaction records of account balance adjustments
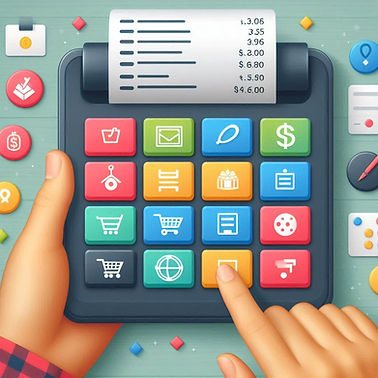
M11. Project Management
Manage New Product Development and Other Projects
-
Project team composition
-
Schedule setting and tracking
-
Design and stage review
-
Overview of all project statuses
-
Verification and approval documents for each stage
-
Budget management
-
Related income and expense management
-
Project profit and loss analysis

M12. Customer Service Management
Record Customer Complaints Related to Production Defects for Company Improvement and Performance Statistics
• Record related improvement methods, follow-up actions, and future prevention decisions
• Link related return records
• Quick search function
• Quickly track work order batch number or purchase warehouse records by shipment order or order

M13. Human Resource Management
Manage Leave, Attendance, Overtime, and Attendance
• Salary setting
• Salary calculation
• Integrate attendance data from card reader
Personnel Administration
• Employee basic data file
• Employee salary master file
• Employee organization affiliation data
• Employee work schedule
• Employee master file that complies with legal regulations
• Related data groups that should be changed when employee changes (new hire, promotion, resignation, transfer, etc.)
• Automatically record and track database record changes, including date, time, user who changed, information before and after a certain period (change log)
• System security control, which can assign different data access rights according to user level. Users can query or modify some data according to their permission settings
Organizational Management
• Establish the company's organizational structure, including organizational units, positions, and employees
• Establish subordinate structure, which can be used as the basis for workflow and data access rights settings
• Establish detailed information of organizational units, such as cost center, working hours
• Establish the structure of work and positions, such as job description, job evaluation, cost center, working hours
Time Management
• Establish different shift modes and generate annual work calendar for employees
• Establish various types of leave (such as annual leave, flexible leave, personal leave, marriage leave, etc.), leave calculation methods and the number of hours employees should have
• END-USER enters attendance and absence data, and the process is automatically approved (Work Flow)
• END-USER enters business trip and expense application and automatically approves (Work Flow).
• Integrate attendance data from card reader
Salary calculation
• Establish different overtime pay calculation methods for different periods, eligible employees and overtime hours restrictions
• Transfer the benefits generated by attendance and absence to the salary system for processing
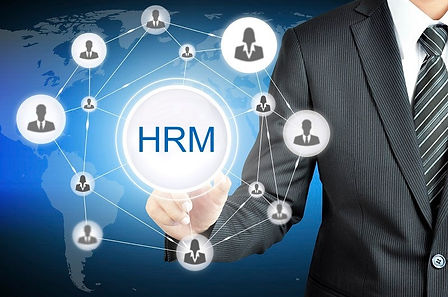
M14. Material Management
Each product category can allow users to define their own accounting subject parameter settings.
• Provide automatic material coding function.
• Provide material barcode number and product image file management requirements. It is convenient to directly enter the barcode when the material is in and out.
• Define whether to control the inventory quantity when the transaction operation occurs.
• Define the attributes of each material as purchase items, self-made items, entrusted items, virtual items, Feature items, Option items, etc. for the benefit of production and material management MRP calculation and material management.
• QR code label printing (material, batch number, asset and pallet/container)
M15. Material Requirements Planning (MRP)

The system obtains the "raw material demand" summary table based on the raw material demand time and quantity derived from the estimated order
• The system consolidates the raw material demand based on the existing inventory, work order reservation, scheduled purchase, and in-transit quantity
• Users decide the "raw material demand" for this MRP project planning based on the above material demand
• Users arrange related suppliers and purchase quantities according to price, raw material quality and customer demand
M17 Advanced Planning & Scheduling (APS)
Automatically generate work order batches (Lot) and related machine schedules according to available machines and work order delivery dates.
-
Allow planners to quickly combine production-related information, such as orders (Order), work orders (MO, or work orders), routes (Route), semi-finished products (WIP), inventory (Stock), material lists (BOM), etc.
-
Adjust according to abnormal situations such as material shortage, shutdown, insertion, quantity adjustment, delivery adjustment, overtime setting, etc.

M18. Production Management
Record the detailed production status of the field staff to grasp the production progress
• Statistics of various manufacturing defect rates
• Grasp the machine scheduling status
• Grasp the attendance status of personnel
• Statistics of work performance
• Provide actual cost analysis information
M19. Warehousing Management
Instant/specific day inventory query, complete record of
material flow and flow reasons
• Instant inventory/cost, customer inventory and inventory availability
• Account inventory
• Overdue inventory quantity and amount
• Future change amount
• Vendor price inquiry
• Historical warehouse entry and exit details (borrowing, borrowing inquiry, batch number inventory, batch number change)
• Material/consumable consumption statistics of each department
• Inventory age table
• Item replenishment suggestion table
• Sales value table, purchase value table
• Batch number inventory age analysis table
Provide a complete equipment integration interface to achieve a paperless work environment
• RF radio system
• Barcode system
• Automated warehousing
• Sorting system
• Electronic tag picking system
Warehouse entry and exit document type description
• Order shipment: Record order shipment and print as accompanying sales order
• Sales return: Record shipment return record, which can be linked to shipment record
• Sorting: Summarize all items to be shipped, assign responsible personnel, and proceed with sorting operations, and turn into shipping orders
• Purchase warehouse entry: Record purchase warehouse entry
• Purchase return: Record purchase return record, which can be linked to warehouse entry record
• Picking: Record the materials required for work order or logistics processing, including internal processing and outsourcing
• Return: Record the return after work order or logistics processing, including internal processing and outsourcing
• Manufacturing warehouse entry: Record the finished product warehouse entry after work order or logistics processing
• Transfer warehouse entry and exit: Record the transfer of materials between warehouses/storage locations
• Inventory adjustment: Record the correction of material inventory, which can be linked to specific documents to explain the source of correction
• Scrap: Record the scrap of materials
• Inventory: Record the inventory details and adjustment of warehouse entry and exit quantities of materials
• Reorganize warehouse entry and exit (unpacking, unpacking, assembly)
• Internal use: Record the use of materials, consumables or machinery and equipment
• Borrowing: Record the borrowing of materials, consumables or machinery and equipment
• Return: Record the return of materials, consumables or machinery and equipment, which can be linked to internal use records or borrowing records
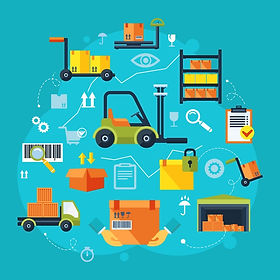
M21. Shipping Management
Arrange the shipping area allocation and transportation tools according to the shipping date and quantity of each shipping order
• Calculate the required freight according to the user-defined freight calculation method
• Quick search function
• Approval management

M22. Quality Inspection Management
Inspection before the material enters the raw material warehouse
• Manage the output inspection records after the raw material is processed in small quantities
• Manage the inspection results records before the material is sent to the production line for processing
• Manage the user's self-made order to select the process and record the results of related items inspection
• Manage the quality inspection records before the product is manufactured and entered the finished product warehouse
• Quick search function
• Approval management
M23. Exception Management
Manage various internal abnormal situations
• Record related improvement methods, follow-up treatment and future prevention decisions
• Quick search function
• Approval management

M24. Asset Management
Asset scanning: QR code continuous scanning and quickly generate warehouse entry and exit orders (including asset details)
• Provide asset management inventory report and location
• Manage the current value of internal assets
• Fixed depreciation operation every month
• Assets can be added, improved, scrapped, depreciated, sold, and other value changes
• Automatically transfer vouchers for asset value changes
